Si3N4 粉末は、窒化ケイ素ボール
を製造するための主原料です。適切な処理方法を選択して、規則的な形状と均一な粒度分布を備えた粉末を得ることが、Si3N4 セラミック ボールの成形、焼結、加工などのプロセスを安定して実行するための基礎となります。
異なる噴霧法によると、Si3N4 粉末の噴霧造粒法には主に遠心噴霧造粒、加圧噴霧造粒、二流体噴霧造粒が含まれます。加圧噴霧造粒 均一なSi3N4粉末を含むスラリーを高圧下で造粒塔内に噴霧して霧化し、熱風により液滴を速やかに乾燥させて球形の粉末とすることで、スラリー中の各種成分の凝集・沈降を防止します。粒子表面の溶媒の揮発速度を制御することにより、規則的な粒子形態が得られ、均一な粒度分布、良好な流動性、適度なゆるめ密度を備えた噴霧造粒粉末を充填することができる。したがって、粉末充填金型の性能が向上し、ブランクの密度と均一性が向上します。したがって、Si3N4 セラミック ボールの特性に及ぼすスプレー造粒粉末のゆるやかな密度の影響を研究するために、加圧スプレー造粒法が選択されました。[7]。
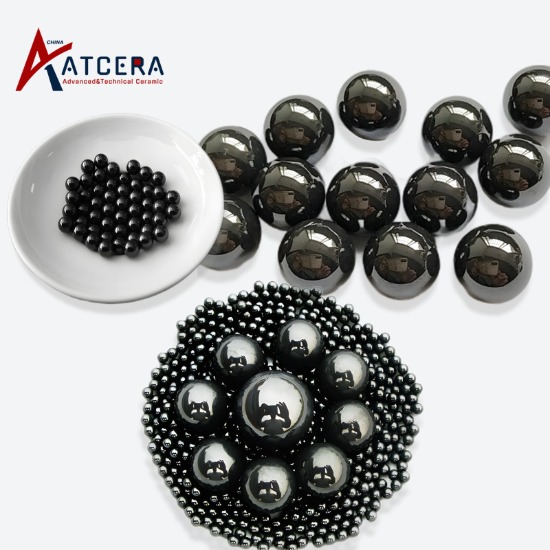
試験材料
Si3N4粉末(粒度分布における累積体積分率が50%の場合、相当粒径D50=1.5μm、α-Si3N4含有率93%、純度99.9%)、Y2O3粉末(D50=1.8μm、純度99.9%)、Al2O3粉末(D50=2.2μm、純度99.95%)など
サンプルの調製
Si3N4→Y2O3→Al2O3=92%→4%→4%(質量比)に従って、混合物をボールミルに加え、無水エタノールを溶媒として使用し、Si3N4ボールを溶媒として使用しました。混合分散用粉砕媒体は24時間、Si3N4ボールと混合粉末の質量比は3:1とした。均一混合後のスラリーの固相質量分率は55%、粘度は4000MPa・sであった。噴霧乾燥塔の入口温度と噴霧板の直径を制御することにより、異なるゆるめ密度の造粒粉末が得られた。 Si3N4 噴霧造粒粉末を乾式プレスで直径 8.731mm のセラミックペレットに加圧し、1850℃で常圧焼結を行った。加熱速度は 3℃/min、保持時間は1.5時間、窒素圧力は9MPaであった。調製後に特性を試験した。
結果
同じバッチスラリーを使用して異なる噴霧造粒プロセスによって調製された造粒粉末のスクリーニング画分データとゆるめ密度を表1に示します。セラミックペレットブランクの密度、焼結密度、曲げ強度、圧砕荷重、破壊靱性およびビッカース硬度異なるゆるめ密度を有する噴霧造粒粉末によって圧縮されたセラミックペレットを表2に示す。
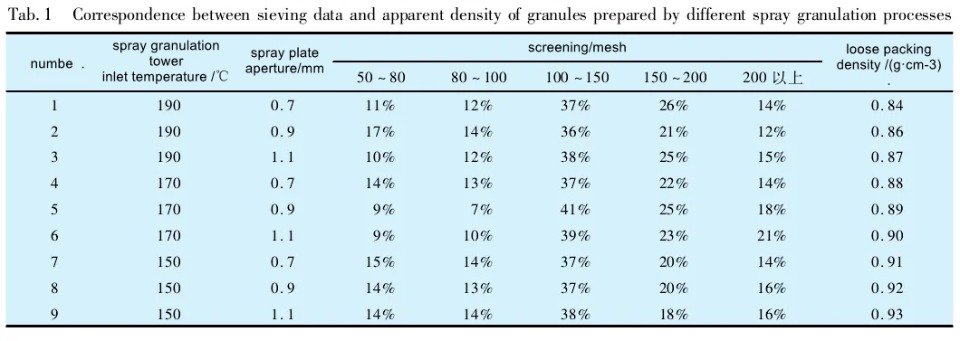
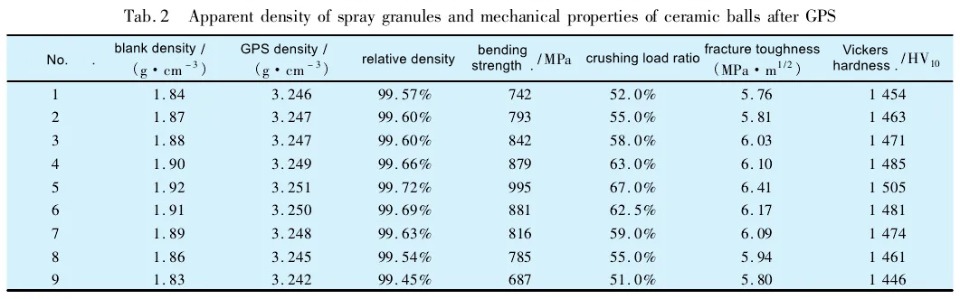
5# 造粒粉末でプレスされた Si3N4 セラミックボールの機械的特性は最高です。ゆるみ密度が高すぎるか低すぎると、粉末のプレス性能と Si3N4 セラミック ボール ブランクの密度に影響を及ぼし、Si3N4 セラミック ボールの機械的特性に影響を及ぼします。そのメカニズムは、ゆるい密度がプレス後のスプレー造粒粉末の気孔率に直接影響し、ガスが排出されにくくなり、焼結プロセス中の粒子や物質の移動距離が長くなり、焼結緻密化に寄与しないためです。
5# Si3N4 スプレー造粒粉末の粒子形態は固体で球形です (図 1)。
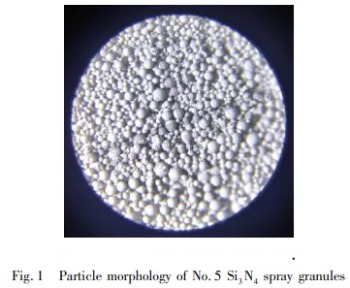
1#〜9#のスプレー造粒粉末によるSi3N4セラミックボールGPSの微細構造を図2に示します。造粒粉末のゆるやかな密度の増加に伴い、GPS後のSi3N4セラミックボール内の細孔の数は最初に増加し、その後減少します。 、Si3N4セラミックボールの密度は最初に増加し、その後減少します。
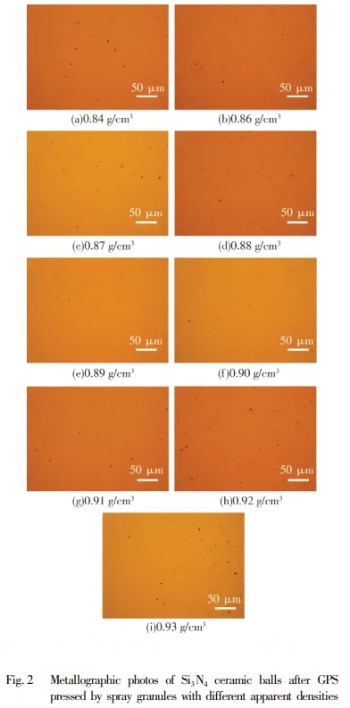
SEMを使用して、最良の機械的特性と劣った機械的特性を有するSi 3 N 4 セラミックボールの粉砕サンプルの微細構造と粒子破壊形態を観察した。図 3 に示すように、Si3N4 セラミック ボールの密度は最初に増加し、その後、造粒粉末のゆるやかな密度の増加に伴って減少しました。ゆるみ密度が高すぎたり低すぎたりすると、不均一な粒子の成長や内部細孔が発生します。
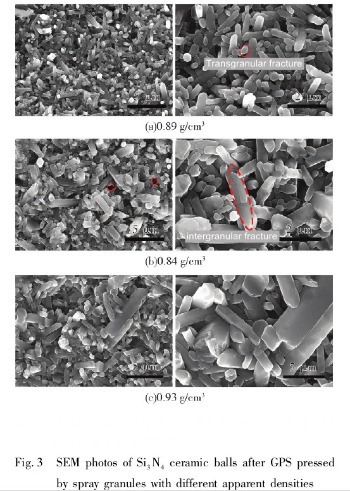
結論
原料としてSi3N4粉末、焼結助剤としてY2O3およびAl2O3を用いて、セラミックボール焼結の緻密化および機械的特性に及ぼすスプレー造粒粉末の緩め密度の影響を分析した。次の結論が導き出されました:
1) Si3N4 セラミックボールブランクの密度は最初に増加し、次に造粒粉末のかさ密度の増加に伴って減少します。ルーズパッキング密度が 0.89g /cm3 の場合、Si3N4 セラミックボールは最高の緻密度と最高の機械的特性を備えます。[49]
2) スプレー造粒粉末のかさ密度が 0.89g /cm3 の場合、形成された Si3N4 セラミックボールは最も小さい細孔、均一な粒径を有し、主に粒内破壊モードを採用します。