ハイテク材料の分野では、優れた熱伝導性、電気絶縁性、機械的強度に優れた窒化アルミニウム(AlN)セラミックスが、エレクトロニクス実装、パワーエレクトロニクス、マイクロ波通信機器などの主要分野のコア素材となっています。 。ただし、窒化アルミニウム基板の準備は複雑なプロセスであり、焼結プロセスと焼結添加剤の選択が最終製品の特性に重要な影響を与えます。この論文では、Alnセラミック基板の製造プロセスから始めて、焼結助剤の選択と基板の性能に対するそれらの影響について詳細に議論し、フロンティア研究と組み合わせて、窒化アルミニウム基板の総合的な性能を向上させる方法について説明します。焼結助剤を最適化することで焼結プロセスを解析します
。
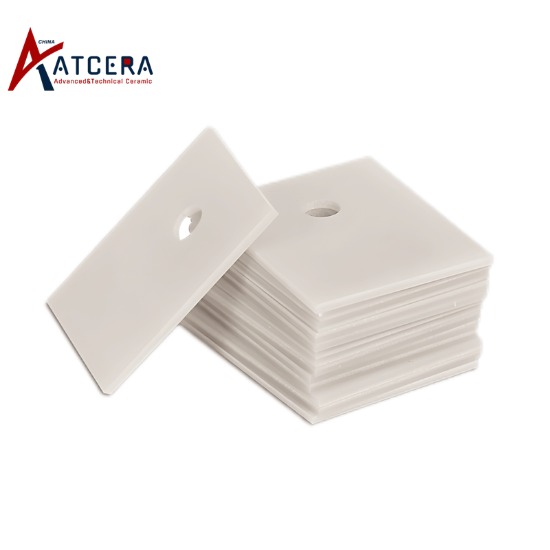
窒化アルミニウム基板の作製技術
窒化アルミニウム基板の準備には、主に原料の準備、混合、成形、焼結およびその他の重要なステップが含まれます。
1.原料の準備
原料の準備は窒化アルミニウムセラミック基板の準備の最初のステップであり、主に窒化アルミニウム粉末、アルミナ粉末、および添加剤の選択と比率が含まれます。主原料となる窒化アルミニウム粉末には、高純度、小粒径、大きな比表面積、低炭素、低酸素といった特性が求められます。アルミナ粉末は通常、焼結プロセス中に低融点複合酸化物を形成し、窒化アルミニウムセラミックスの緻密化を促進するための焼結助剤の一部として使用されます。添加剤は、材料の成形特性、焼結特性、および機械的特性を調整するために使用されます。
2.混ぜて成形
混合工程では、その後の成形の均一性と安定性を確保するために、窒化アルミニウム粉末、アルミナ粉末、添加剤を一定の割合で混合する必要があります。混合は乾式または湿式で行うことができます。成形は通常、プレス成形、射出成形、金型成形などによって行われ、混合された原料を一定の形状と大きさのビレットに作ります。
3. 焼結
焼結は窒化アルミニウムセラミック基板の準備における最後のプロセスであり、最も重要なステップです。高温条件下で、ビレット内の粒子が焼結によって結合され、緻密なセラミック基板が形成されます。焼結プロセスでは、セラミック基板の成形品質と性能を確保するために、温度、雰囲気、時間を制御する必要があります。一般的に使用される焼結プロセスには、ホットプレス焼結、非プレス焼結、マイクロ波焼結、放電プラズマ焼結、および自己伝播焼結が含まれる [28] 。
焼結助剤の選択と基板の特性に及ぼす影響
焼結助剤は窒化アルミニウムセラミック基板の製造において重要な役割を果たします。これらは窒化アルミニウム粒子表面のアルミナ組成物と反応して低融点の複合酸化物を形成し、焼結体中に液相が形成される。これらの液相は窒化アルミニウム粒子を取り囲み、毛細管力の作用により粒子の再配列と内部細孔の放出が起こり、最終的に窒化アルミニウムセラミックスの緻密な焼結が実現します。
1.一般的に使用される焼結助剤
窒化アルミニウムセラミック基板に一般的に使用される焼結助剤には、CaO、Li 2 O、B 2 O 3 、Y 2 O 3 、CaF 2 、CaC 2 およびCeO 2 が含まれる。これらの材料は焼結プロセスにおいて二重の役割を果たします。まず、窒化アルミニウム粒子の表面で酸化アルミニウムと結合して液体アルミン酸塩を形成し、物質移動を加速して焼結を促進します。第二に、それらは酸素と反応して格子酸素含有量を減らし、窒化アルミニウムセラミックの熱伝導率を高めることができる[40]。
2. 焼結助剤の選定原理
焼結助剤を選択する場合、窒化アルミニウムセラミック基板の特性に及ぼす影響を考慮する必要があります。一方で、焼結助剤は窒化アルミニウムセラミックの緻密化を促進し、熱伝導率と機械的強度を向上させる必要があります。一方、焼結助剤は、窒化アルミニウムセラミックスの電気絶縁特性や化学的安定性に影響を与えないように、過剰な不純物の導入を避ける必要があります。したがって、焼結助剤を選択する場合、最適な焼結助剤の配合を決定するには、多くの実験と最適化が必要です。[46]
3.基材の性能に対する焼結助剤の影響
焼結助剤の選択と含有量は、窒化アルミニウムセラミック基板の性能に大きな影響を与えます。たとえば、一般的に使用される焼結助剤の 1 つである Y2O3 は、その含有量が適度であれば、窒化アルミニウムセラミックの熱伝導率と曲げ強度を大幅に向上させることができます。ただし、Y2O3の含有量が多すぎると、Y-Al-O相が形成され、熱伝導率が著しく低下する。したがって、窒化アルミニウムセラミック基板を製造する場合、最高の性能を得るために焼結助剤の含有量を正確に制御する必要がある[52]。
AlN基板の性能向上
さまざまな応用分野における窒化アルミニウムセラミック基板の性能に対する高い要件を満たすために、研究者は常に新しい焼結添加剤を探索し、焼結プロセスを最適化し、新しい調製技術を開発しています。
1.新規焼結助剤の開発
窒化アルミニウムセラミック基板の性能をさらに向上させるために、研究者は新しい焼結助剤の開発を積極的に行っています。たとえば、希土類元素や遷移金属元素を導入することにより、窒化アルミニウムセラミックスの格子構造を最適化し、熱伝導率や機械的特性を向上させることができます。さらに、複合焼結助剤を使用することでさまざまな特性を実現できます[64]。
2.焼結プロセスの最適化
窒化アルミニウムセラミック基板の性能を向上させるには、焼結プロセスの最適化が鍵となります。焼結温度、保持時間、雰囲気を調整することで、窒化アルミニウムセラミックスの微細構造を正確に制御できます。例えば、マイクロ波焼結や放電プラズマ焼結などの急速焼結法により、焼結時間を大幅に短縮し、生産効率を向上させることができます。同時に、焼結雰囲気中の酸素含有量と温度勾配を正確に制御することによって、窒化アルミニウムセラミックスの微細構造と特性をさらに最適化することができます。[70]。
3.調製技術の革新
前処理技術の継続的な開発により、研究者は窒化アルミニウムセラミック基板の性能を向上させるための新しい前処理方法を常に模索しています。例えば、窒化アルミニウムセラミック基板の精密な作製は、鋳造成形や射出成形などの高度な成形技術を使用することで実現できます。さらに、窒化アルミニウムセラミック基板の溶接性能、安定性、耐食性は、無電解銅めっき、セラミック基板の封止、およびその他の後処理プロセスによってさらに向上させることができる[76]。
結論
要約すると、窒化アルミニウムセラミック基板の調製と焼結助剤の選択は、その特性に重要な影響を与えます。窒化アルミニウムセラミック基板の総合的な特性は、焼結助剤配合の最適化、焼結プロセスの改善、および新しい製造技術の開発によって大幅に改善できます。今後、材料科学と製造技術の継続的な発展により、窒化アルミニウムセラミック基板の応用分野はさらに拡大し、電子パッケージング、パワーエレクトロニクスデバイス、マイクロ波通信機器の開発を強力にサポートするでしょう。同時に、新技術や新材料の開発動向にも細心の注意を払い、常に研究領域を拡大し、窒化アルミニウムセラミック基板技術の継続的な進歩と革新を促進する必要があります。